Our Practices
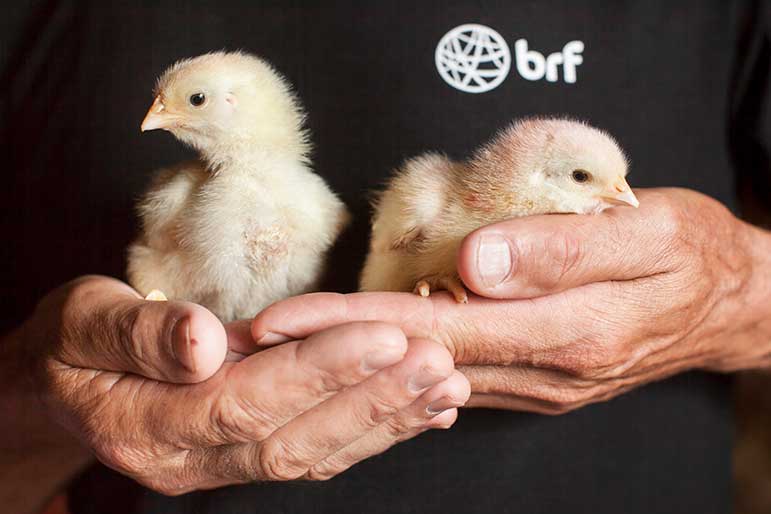
In addition, in order to adopt best practices, the company guarantees constant training for teams of managers, technicians, producers, drivers and operators, as well as improving the production process, including handling, nutrition and health care.
LEARN MORE ABOUT OUR ACTIVITIES
Our animals are not genetically
modified and do not receive hormones at
any stage of our breeding system.
Medications and vaccines are handled only on the advice of our veterinarians, through an on-site visit to assess the clinical condition of the batch in production, in line with guidelines defined internally by the company and its specialists, and legislation and client standards.
The contract between BRF and the integrated producers determines that any intervention in pthe production lot must be carried out only by the company, including any treatment, even if it is not medicinal. The company also has a network of laboratories that assists in the identification of the causes of problems with the lots, as well as expedites the decision making, through the fast result.
BRF does not make prophylactic use of antibiotics in the production of poultry and always seeks continuous improvements of the processes, allowing the gradual reduction of drug use throughout the chain. Most BRF poultry production is already produced without antibiotic growth promoters. By the end of 2018, 100% of the production of all animals in the chain will be free of antibiotic growth promoters (AGP-Free). In addition, BRF has reduced the use of antibiotics considered by the World Health Organization (WHO)as critical for use in human medicine.
In order to advance in welfare actions, we have part of our production working with continuous practices of environmental enrichment. Protocols have been developed and different objects are being tested to identify mechanisms that stimulate the natural behavior of our animals, contributing to the reduction of stress and the improvement of health conditions, such as:
• Internal evaluations using perches, sawdust bales and other picking instruments are present on several farms of our integration of turkeys and chickens.
BRF has specific indicators that assess farm performance and slaughter procedures, including indicators of animal welfare at each stage of production, which are constantly improving. There is continuous monitoring of mortality, animal weight gain, stocking density (live weight or number of animals per square meter in a facility), disease occurrence, mean animal transport time, and pre-slaughter desensitization , acting with corrective actions when necessary.
A checklist that includes indicators of animal welfare, such as gait score, injuries and cleaning of animals, is applied to 100% of our own and integrated farms in Brazil, being a reference for our internal checks and development of specific action plans.
We have a Corporate Committee for the Transportation of Live Cargoes that carries out the monitoring of the agricultural transport indexes. In the countries where we have agricultural production, transportation time is still a great challenge, given the territorial dimensions of each locality (like Brazil). As a way to mitigate stress in transportation, we have the commitment established in the internal corporate guidelines that define the maximum recommended time for transporting the animals. Trucks have trackers for pre-determined speed and route control and drivers are periodically trained.
BRF also adopts the premises of humanitarian slaughter, reinforcing its concern for animal welfare at this relevant stage of the process. 100% of the animals are desensitized before slaughter, respecting religious specifications when requested by the market, as is the case of the precepts of halal slaughter.
We constantly train our employees on animal welfare topic, such as:
• More than 400 employees sensitized to the topic in structured programs and knowledge sharing on animal welfare in day to day activities.
• In 2017, 100 collaborators in the Humanitarian Abatement Program, recognized by the Ministry of Agriculture, Livestock and Supply (MAPA), as part of the partnership actions with the WAP NGO. In 2018 training is planned for an additional 100 employees.
• 100% of our chicken and turkey integrators and the BRF team are trained in winter and summer management, in which the theme of animal welfare is strongly addressed.
• 100% of picking teams and drivers undergo training on best practices to ensure the welfare of the birds in the process of loading on the farms and transport.
• In 2017, more than 900 farmers and employees and more than 200 BRF extension workers were trained in Modules 1 (well-being at all stages on the farm) and 2 welfare in the pre-loading, loading and unloading of animals for slaughter) of the association’s animal welfare program.
• Chicken Academy, a training program for the continuing training of BRF technicians and extension workers, carried out local field team training in 2017. We gathered approximately 300 people from all units in Brazil and Argentina. With content divided into four modules – Health, Incubator, Matrices and Broiler Chickens- we discuss the most relevant topics for all areas, with the objective of promoting interaction and expansion of the vision of the production process and offering management tools to leverage processes and people .
We have also developed partnerships with universities and researchers to develop sustainable production practices that meet the well-being of production animals, as well as the promotion of technical meetings for discussions that foster knowledge outside the company.
KNOW SOME PRACTICES DIFFERENTIATED BY SPECIES:
BRF, considering its principles of offering conditions of welfare to the animals of its creations, works densities suitable for the different species and categories, being inferior even to the international standards more rigorous. Therefore, all poultry have space to move freely, with the possibility of exercising natural behavior, such as: scratching, bathing in sand, swallowing and flapping of wings.
For example, in 55% of chickens raised by the company, which is focused on the production of light birds, the density practiced is less than 32kg / m². Currently, of the 23 units that BRF operates with broiler chicken in Brazil, 8 work with a final density of less than 30 kg / m2, that is, more than 30% of the units, which in the first half of 2018 represented around 48 % of birds slaughtered. BRF unit in Thailand operates 100% of the facilities with a density of less than 30 kg / m².
All birds have continuous access to water of sufficient quality and quantity to have their best development and 100% of the farms have water meters by which the water consumption is monitored. The records are kept and, in case of deviations, they are corrected daily. Water quality is constantly monitored by measuring chlorination and constant flushing, helping to maintain the ideal temperature.
Comfort and environmental enrichment are basic principles of the breeding environment of our poultry. To do so, we use good quality aviary bed and adopt as a metric about 15 cm deep for turkeys and 10 cm deep for chickens and we handle constantly so that it is always fluffy and dry. Whenever necessary, the bed is renewed, as well as providing thermal comfort, it favors the poultry natural behaviors. Every bed (made of shavings and / or rice hulls) comes from an approved supplier, guaranteeing controlled quality, free of contaminants.
For the maintenance of the thermal comfort conditions of the animals, heaters, fans or hoods, evaporative panel and / or nebulizers are used in the breeding environment. The maximum and minimum temperatures and humidities of the installation are recorded daily for control and maintenance of the adopted standards.
We also understand how important light management is for birds. Therefore, we respect the minimum of 8h of light a day and 4h of dark, following the day / night rhythm and the appropriate light intensity for each phase in each breeding system.
The process of pre-slaughtering of animals follows specific legislation and internal rules. For this process, 100% of the animals are desensitized and the Company also attends cultural, religious (such as the Halal for slaughter guidelines), markets, customers and certifications specificities – which are often higher than the current legislation .
Implantation of the infrared in 100% of the production of turkeys, as well as of matrices of chicken of cut, for the accomplishment of the debicagem, replacing the traditional system of cut and cauterization. The deboning is done in only 1/3 of the nozzle.
CHICKEN
About 40% of the production process takes place in conventional aviary systems, which are facilities that work with open curtains using the maximum of the natural condition of the environment with the use of natural daylight. The other installations operate with controlled environment systems, which allow greater control over extreme environmental variables such as temperature, humidity and illumination.
The transportation of the chickens is done following the guidelines of the Corporate Committee of Live Cargo Transport. Currently 100% of the chickens that go to slaughter are transported regularly in a maximum period of up to 8 hours.
As an innovative and unique process in Brazil, a pilot project was implemented at the Marau unit (RS), for pre-slaughter desensitization using gas, reinforcing our commitment to humane slaughter.
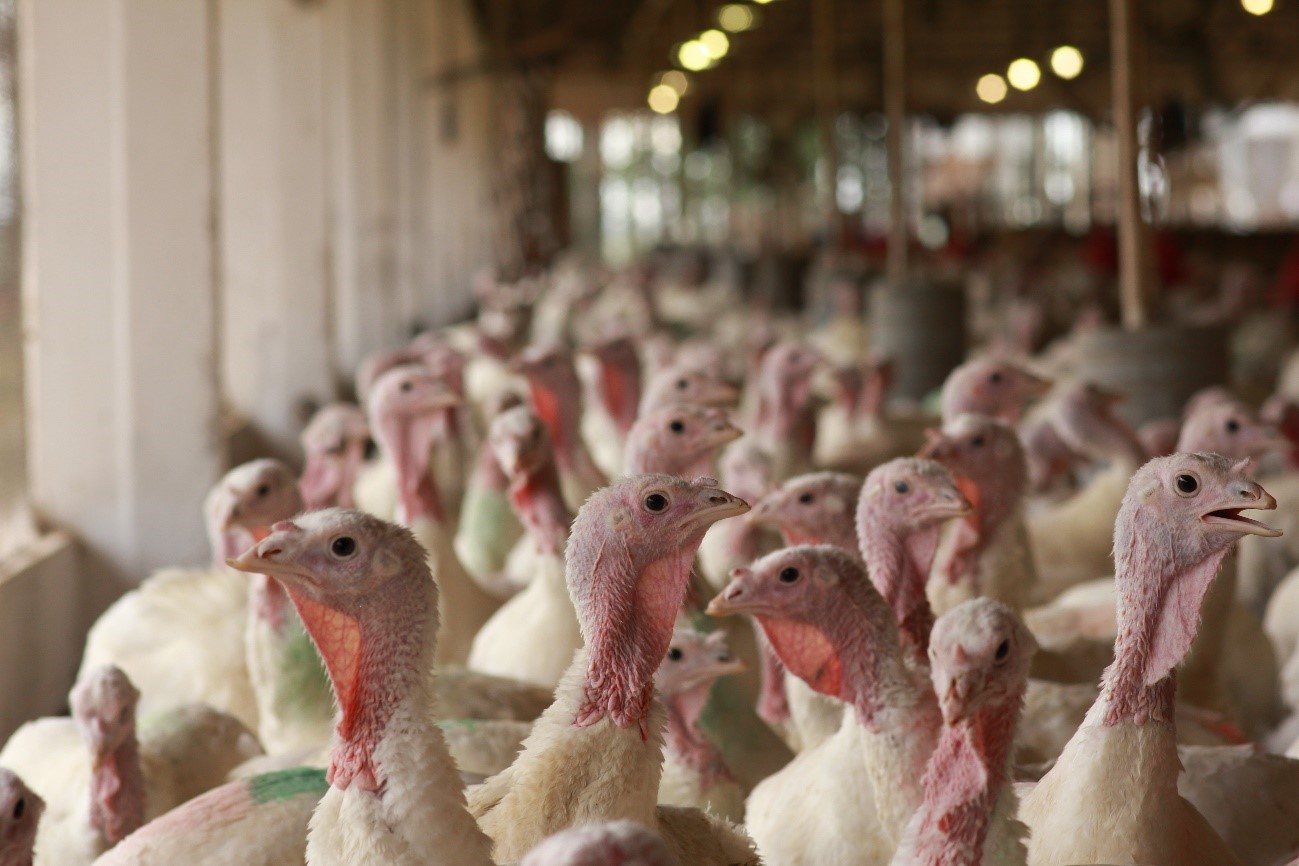
TURKEYS
About 50% of the production process takes place in conventional poultry systems, which are facilities that work with open curtains using the maximum of the natural condition of the environment. The other facilities operate with a differentiated controlled environment system, which allows greater control over the extreme environmental variables, such as temperature and humidity, but which allow the entrance of natural light through its curtains. Therefore, 100% of the turkeys are raised with natural lighting.
The transport of the turkeys is done following the guidelines of the Corporate Committee of Live Cargo Transport. Currently, 70% of the turkeys that go to slaughter are transported regularly in a maximum period of up to eight hours.