Production Chain
Safety and quality are premises that BRF values in all stages of the development of its products. And it is only through a series of integrated and consistent operations that you can ensure that these attributes are controlled and applied throughout the process.
With a full integration structure, called Vertical Integration, all points in the chain are BRF’s control and responsibility. In this way, the company can guarantee the quality and safety of products and manage its entire chain, from start to finish. This structure, of which the integrated producers are included, still includes:

Poultry Chain: poultry farm of poultry stock > hatchery > farmhouse > egg production farm > hatchery > integrated (fattening) > slaughtering > processing.
From there, the whole process is done in our processing plants, which are the places where the raw materials are processed and transformed into products . It is only with the management of this structure that we can guarantee quality at every stage.
INTEGRATED PRODUCERS: THE START
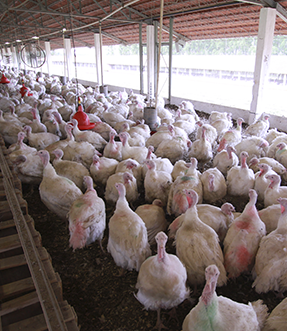
They are the ones who start our chain. BRF provides the integrated producer with animals, food, technical assistance, transport, slaughter and all the products necessary for the rearing of animals. On the other hand, the producer provides facilities that meet the hygiene, labor, welfare and quality of life of animals.
From then on the whole process is following accompanied and controlled so that the products comply with the legislation of Brazil and other countries around the world. Among the main items of care are:
The produced animal feed follows strict quality criteria, with standards defined by specialized nutritionists.
The ingredients are assessed to their composition and quality and only the allowed items for use in animal feed can be used. The animal feed are mainly composed of corn and soybean meal and are nutritionally balanced, with a quantity of food calculated to provide – and guarantee – the minimum requirements of nutrients and vitamins for the animals at different stages of their life.
In addition, the factories follow specific legislation on good feed production practices and are subject to MAPA inspection (Ministry of Agriculture, Livestock and Supply).
All support for the correct animal breeding is provided by the BRF technical team. Any necessary medication is applied only with prescription, after the visit of the veterinarian and diagnosis of disease, always respecting the precepts of animal welfare and the sanity of the lot, which is the set of characteristics that constitute the health of the animals, guaranteeing total quality.
The control of production indicators is carried out on a regular basis throughout the chain and recorded in the Batch Tracking Sheet (FAL). This fact sheet is extremely important, since it functions as a journal, with the registration of all the information related to the development of the animals, products used, vaccines, ration received and the guidelines of the extensionist. In addition, all FALs are sent to the SIF (Federal Inspection Service) for a conference at the time of slaughter of the animals. Such data are important for traceability, since, in this way, we are able to know all the information pertinent to the batch. It is worth mentioning that only BRF, the producer and the SIFs have access to this document.
BRF still has complete control of the withdrawal periods – phase necessary so that the meat does not present any product residue in case of medication.
Here are some of the key controls performed during production:
• Mortality: how many poultry die and why. In this way, in case of high mortality, the farmer can call the extension worker to verify what may be happening.
• Water Consumption: constant monitoring of the daily water consumption of the lot, an action whose monitoring is important for an immediate intervention, if it is verified that the lots are passing headquarters.
• Feed Intake: constant monitoring that the poultry are ingesting the right amount and type of feed and, if necessary, take immediate action if any change is observed.
• Weight Gain: measured weekly, allows you to check if the batch is developing satisfactorily. If there is any non-compliance, the extension agent can take the necessary actions.
• Temperature Inside The Installation: daily action to monitor temperature and maximum and minimum humidity. The procedure is important to verify and provide thermal comfort for the poultry. In case of deviation it is possible to intervene quickly.
All national and global standards and procedures used to prevent the introduction of infectious diseases at any place of production are strictly followed by BRF.
All producers follow the Good Manufacturing Practices, manual prepared by the Wow our team of specialists, composed of veterinarians, zootechnicians and agronomists. In addition, they are trained in animal welfare processes and monitored by BRF extension workers throughout the life of the lots, as well as in loading and transport.
In order for animals to develop well, in a safe and appropriate environment, a series of measures are taken, including: hand washing before contact with animals, pest and vector control, use of appropriate footwear, control of the destination bedding and products used during the batch. In addition, producers comply with the local laws required and only authorized persons have access to the premises. Authorized visitors must fill out the “Visitor Control” document attesting to their health.
BRF is certified in the GlobalGAP, Alo Free e Certified Humane standards in some units, such as: Chapecó, Marau, Capinzal, Mineiros and Serafina Corrêa. The company also serves internationally recognized clients for the high quality standards required of its suppliers. Currently 100% of the BUG Buriti Alegre (GO) produces certified broilers in the Certified Humane standard.